Traditional Isolation Gown & Surgical Gown Production Line
Traditional production of isolation gowns and surgical gowns requires a massive workforce, entailing manual cutting, welding, and folding of each piece. This extensive process raises notable concerns. Manual labor introduces challenges in maintaining quality control. Productivity is constrained, making the production process susceptible to errors. Ineffective resource utilization commonly results in material wastage.
TAROMED Fully Automated Production Line
Our AI-driven fully digitalized automated production line ensures that the entire product manufacturing process is contactless, with workers primarily responsible for operating machines and conducting inspections. advanced machinery seamlessly cuts, welds, and folds each piece with precision. The result is a streamlined process that not only ensures consistent quality but also significantly boosts productivity. Our automated system minimizes the risk of errors and material wastage, leading to a more efficient and sustainable manufacturing approach.
- Production Lines are developed, designed and manufactured by TAROMED, with independent intellectual property rights and international patents.
- Fully automated preparation, cutting, ultrasonic welding, cuff sewing, production, folding, packaging and quality inspection of isolation and surgical gowns.
- 60,000 Gowns/Day Production Capacity for Smart Factory with 10 lines of production (24h production).
- Size of each line: 30m long, 8m wide, 2.8m high, surface of 89m2 (958sqft)
- Low staff needed: One line of production need 1staff per line per shift only
- Yield Rate: ≥98%
- Energy Consumption: 9.3kWh/Day/Line
- Weight per m2: <270KG/m2
- Production speed: 12s / each
Quality Control of the Entire Product Production Process
How Does AI Forecasted Automation Empower TAROMED's Global Deployments?
Through our advanced system, powered by big data and AI models, TAROMED has unified global management by standardizing and modularizing various factors, while harnessing high-level automation for machinery and processes. This ensures an adaptive and consistent global distribution system. With over 70 patents spanning the United States, Europe, China, and Japan, our dedication to innovation knows no bounds. At TAROMED, our optimal solution lies in the digital management system, which combines production control, smart manufacturing equipment, and automated production lines to deliver high efficiency, flexibility, and reliability. This approach, setting us apart from conventional manufacturing, revolves around swift iterations, driven by automated production lines and a sophisticated workforce management system. This approach not only liberates us from labor constraints but also ensures the continuity and stability of our production. Furthermore, TAROMED leverages its in-house developed logistics tracking and online ordering system to provide transparent and traceable order transactions. In addition, a three-tier network model, orchestrated through the synergy of software, sensors, and machinery, empowers TAROMED to achieve unified management and enhance efficiency in varied global settings.
How Do We Maintain Rigorous Quality Control During the Full Product Manufacturing Cycle?
Taromed implements a rigorous supplier evaluation process, ensuring all raw materials and final products adhere to our certification and manufacturing benchmarks. It’s mandatory for raw materials to undergo factory evaluations based on essential quality metrics. Upon entering Taromed’s facilities, each raw material is given a traceability code. For added assurance, every batch of materials undergoes testing in our labs, with the entire procedure saved to the cloud for subsequent scrutiny. Moreover, for quick reference, samples are always retained and labeled with their respective traceability codes. AI-driven inspection system is implemented to scrutinize the production line and detect any issues related to quality. Continuous video documentation of the manufacturing process is available for remote access, offering transparency. After production, samples are kept for future insights and in-house assessments are diligently documented, including video records of the testing processes. Utilizing the most advanced technology, Taromed’s internal quality standards exceed global benchmarks, ensuring superior product quality.
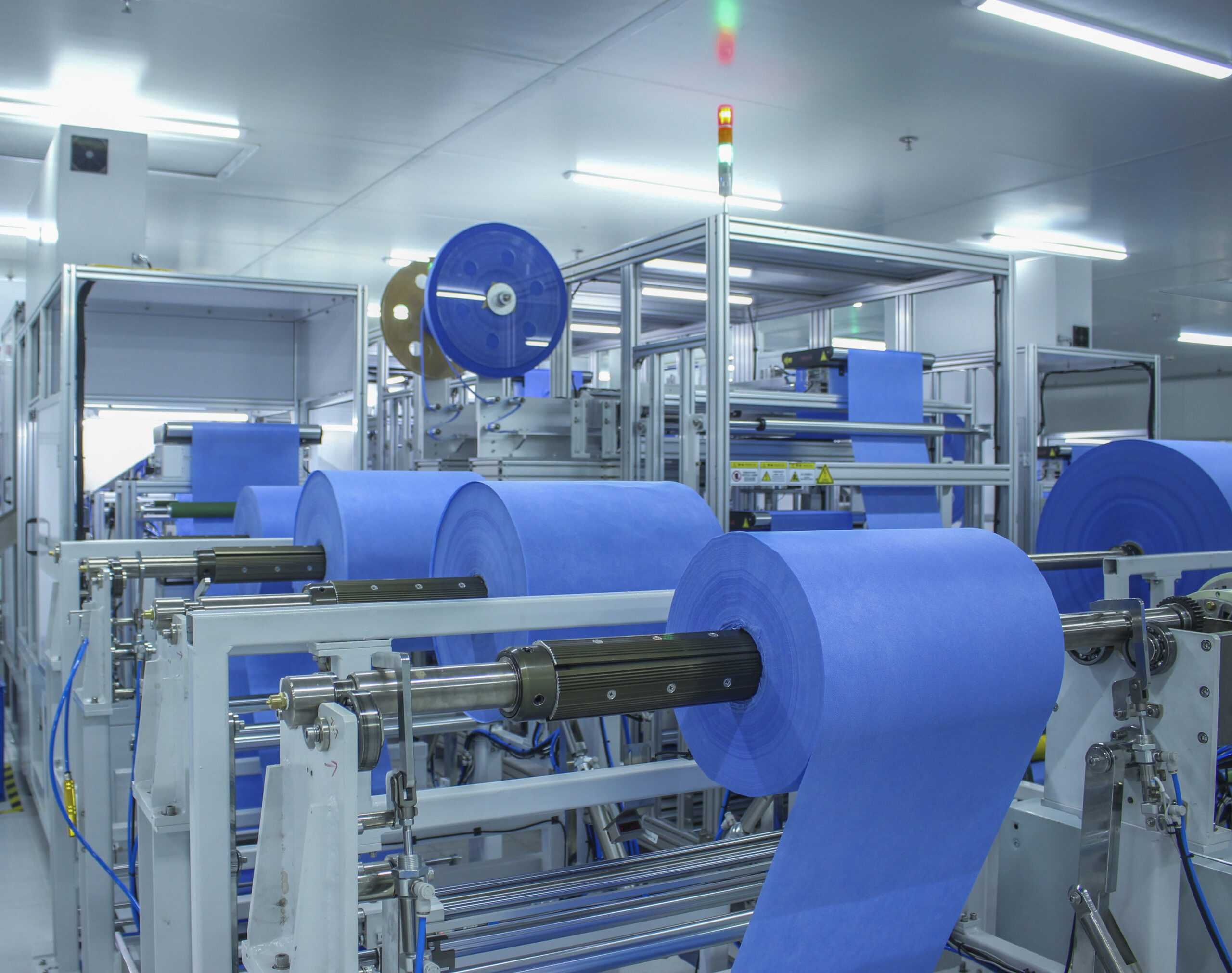
What's the Role of Industry 4.0 Technologies in Strengthening TAROMED?
TAROMED places the core of its operations in a digital management system based on digital twins, spanning from design and production to sales. Optimizing production efficiency at the source maximizes the controllability of the production process, reduces waste in industrial and product materials, and ensures cost control and stable production capacity.
Throughout equipment design and development, TAROMED harnesses digital twin technology to construct virtual, digital models of equipment. These models undergo simulated testing and verification, allowing for continuous performance optimization by simulating changes in various equipment parameters. This approach significantly enhances equipment reliability and availability while mitigating risks and reducing trial-and-error costs in product research and manufacturing.
Within the production line, TAROMED deploys a virtual digital production system by incorporating visual, vibration, and sound sensors, PLC feedback, and artificial intelligence on individual production equipment. This enables the creation of a digital twin of the production line, simulating equipment operations and continuously collecting and intelligently analyzing operational data. Real-time comparisons between the actual and virtual production line statuses allow for the prediction of potential anomalies and optimal maintenance timings, thereby enhancing spare parts maintenance efficiency.
At the management level within the entire physical factory, TAROMED employs digital twins to establish a virtual digital factory. This digital environment facilitates simulations of equipment or production line layout adjustments, spatial function changes, and more, enabling continuous optimization of global factory management to create an optimal factory management system.
TAROMED leads the way in the medical manufacturing industry, actively applying digital twin technology to research and development. Leveraging digital twin technology, it continually refines the layout of production management in the industry, empowering the medical manufacturing sector to genuinely embrace Industry 4.0.